ジャスト・イン・タイムとは? かんばん方式との違いやメリットを解説
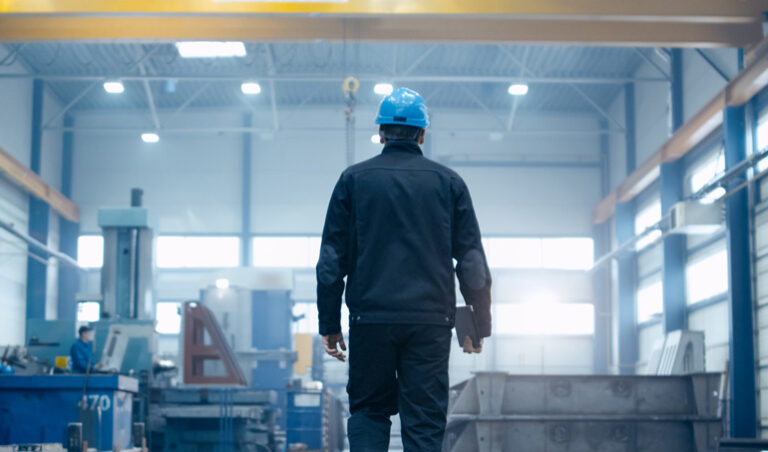
「ジャスト・イン・タイム生産方式(リーン生産方式)」は、トヨタ自動車株式会社(以下、トヨタ)が開発した生産効率を上げる生産管理システムのひとつとして知られています。もともとは製造業を中心として広まった生産管理システムですが、近年では他の業種でも応用されています。
ジャスト・イン・タイムは「必要なものを必要なだけ作る」という方式のため、作業効率を向上することと業務の無駄を省くことが最大のメリットです。その反面、やり方を間違えてしまえば生産がストップするリスクもあります。
今回は、ジャスト・イン・タイムの基礎知識を始め、トヨタ独自の生産方式である「かんばん方式」との違い、メリットやデメリットを解説します。働き方改革や業務効率化が叫ばれる今だからこそ、改めてジャスト・イン・タイムを振り返ります。
トヨタ自動車が導入したジャスト・イン・タイムとは?
ジャスト・イン・タイム生産方式の概要を説明する前に、製造業における生産方式の変遷を振り返ってみましょう。
従来の製造業では、フォード社が広めた「大量生産方式(フォード生産方式)」が主流でした。20世紀初頭に確立されたこの方式は、多品種を生産するのではなく1品種に絞り、ベルトコンベアを利用した流れ作業を実現したことが革命的でした。仕事を単純作業に分解したため作業員の技術を平準化でき、原価を抑えた安い製品を市場に大量供給できるようにしました。一方で、大量生産方式は1品種のみの製造に特化しているため、消費者ニーズの変化に応じた生産品目の柔軟な変更が難しく、売れ残った在庫処理にコストがかかるといったデメリットもありました。
ジャスト・イン・タイムが革新的だった理由
「必要なものを、必要な時に、必要なだけ生産する」と言われるジャスト・イン・タイムは、徹底的に無駄を削減した結果生まれました。海外でもJIT、もしくはリーン生産方式として普及しています。
ジャスト・イン・タイムは、製造業の理想の生産方式と言われています。製造業において、過剰在庫はキャッシュフローを悪化させますし、一方で少ない在庫では機会損失につながります。「必要なものを、必要な時に、必要なだけ生産する」と掲げるのは簡単ですが、実現するのは難しいとされていました。トヨタはこの理想を実現したため、世界に名だたる自動車メーカーの一角に地位を確立できたのです。
ジャスト・イン・タイムには大きく3つの特徴があります。1つ目は、「後工程引取」で、必要生産数に応じて、部材を前工程から引き取ります。2つ目は「工程の流れ化」(後述)。そして、3つ目が「必要数に応じてタクトを決める」ことです。この3つによって、製造ラインを平準化し、無駄を削減し、欠品リスクの低減を実現しました。このジャスト・イン・タイムを実現した背景に、「ニンベンの付いた自働化」と「かんばん方式」と呼ばれる同社独自の手法があります。
ニンベンの付いた自働化
ジャスト・イン・タイムと同様に、トヨタが開発したのが「自働化」です。機械を使う場合は「自動化」と表記されますが、トヨタでは「ニンベン」が付いています。
機械による自動化との違いは、「作業を機械化する」点と「機械を使いながら人も働く」点にあります。自働化では、機械の異常や誤作動、不良品の生産が発生した場合、人が必ずチェックをいれて生産ラインを停止します。それによって後工程に不良品を送ることをなくし、品質管理の面で大きな成果を上げました。「自動化で生まれる一定の不良も最終的にはコスト安になる」という大量生産方式の考え方とは異なり、不良を生産すること=無駄と捉えたトヨタの考え方を「ニンベンの付いた自働化」、もしくはシンプルに「ニンベン」と言います。
かんばん方式
またトヨタは、ジャスト・イン・タイム生産方式だけではなく、独自の生産管理方法「かんばん方式」(スーパーマーケット方式)を考案しました。これは製品名や品番が記載されたカードを用いて製品を管理しているスーパーマーケットのやり方を参考に、各工程での引き取り時に必要となる部品などを「かんばん」でやり取りすることが由来となっています。
かんばん方式は、部品生産時に製品に付ける「仕掛けかんばん」と、部品の引き取り時に付ける「引取りかんばん」の2つがあります。「必要な在庫を必要な分だけ用意する」前工程と「必要な分を持っていく」後工程に見立て運用し、後工程によって減少した在庫を前工程で補充することで、効率化を実現したのです。
ジャスト・イン・タイムのメリットとは?
改めて、ジャスト・イン・タイムのメリットを3つ紹介します。
メリット1.在庫量の適正化
無駄な生産が減ることは、在庫量の見直しにつながります。在庫に余裕をもたせることは、予想を超える発注などへの対応をする上で必要ですが、欠品の不安から過剰な在庫を保持することはキャッシュフローの悪化を招きます。
製品が利益となるのは、生産した時ではなく販売が行われた時です。長期間販売できなかった製品はコモディティ化し、市場価値が落ちて値下げへの判断を迫られます。ジャスト・イン・タイムでは、「必要なものを、必要な時に、必要なだけ生産する」ことが可能となるので、発注に対して適切な生産量、在庫数を維持できます。
メリット2.製造ラインの無駄を省き、効率化を実現
生産を行う際、手持ちの業務がない時の「待ち時間」など、作業員には無駄な時間が発生することがあります。それは資材を入荷するまでの時間や、自分の担当する業務まで生産ラインが進んでくるまでの時間です。ジャスト・イン・タイムでは必要以上の生産を行わず、不要な作業も省いているため、人員に関する無駄が少なくなります。
メリット3.リードタイムの短縮
ジャスト・イン・タイムでは、不要な作業を省くことから、製造から検品までのリードタイム短縮を実現します。生産時のリードタイムが短縮されれば、顧客への納品もスムーズに行われ、販売機会損失の防止や顧客満足度の向上につながります。
ジャスト・イン・タイムのデメリットと前提条件
ジャスト・イン・タイムは、どのような現場でも実現できる生産管理システムではありません。前提条件を満たす現場でなければ、ジャスト・イン・タイムを活用できずに業績を悪化させるリスクも考えられます。では、ジャスト・イン・タイムの前提条件とは、どのようなものでしょうか。
前提1.平準化生産ができる
適切な生産量を実現し、無駄を解消するジャスト・イン・タイムには、「平準化生産が可能な製品に限る」ことが重要な前提条件となります。
現場の無駄が発生するひとつの背景として、「今日は100個生産」、「明日は30個生産」などといった生産量のばらつきが挙げられます。作業量が多ければ作業員に大きな負担をかける一方、作業量が少なければ作業員の待ちの状態が続き、人件費が大きくなります。現場の無駄を解消するためには、適切な生産量とそれに見合った人員で対応することが求められるのです。
前提2.工程の流れ化
工程を停滞させず、余分な在庫や手待ちがない仕組みが構築されていることも、ジャスト・イン・タイムを成立させるためには欠かせません。例えば、1個流し生産や小ロット生産などを取り入れ、整流化を目指すことが求められます。特に複数の業務を担当できる「多能工」は、「必要な時に、必要な場所に、必要な人員を配置する」ジャスト・イン・タイムにおいては必須です。臨機応変な人材配置は、業務量や業務負荷を平準化する上でも不可欠です。
前提3.後工程の引き取り
後工程引き取りとは、必要なものを前工程から引き取り、なくなった分を前工程が補充することを指します。「後工程が必要な分を引き取る」、「前工程がなくなった分を補充する」というふたつの作業を連結させるのが、上述の「かんばん方式」です。「必要なものを必要なだけ作る」ジャスト・イン・タイムには、欠かせない生産管理方法ですので、かんばん方式を採用できない生産はジャスト・イン・タイムには向きません。
前提4.小ロット生産化
ひとつのロットを可能な限り小さくする「小ロット生産化」が実現すれば、工場の稼動時間が短くなると同時に、無駄な在庫を発生させることもありません。小ロット生産化には、機材の切り替えが大きなネックとなります。作業を担当する人員の配置を見直す他、汎用性の高い機材を活用することで、段取りを簡略化、小ロット生産を実現できるヒントとなります。
まとめ~ジャスト・イン・タイムは無駄を削減するためのヒント~
ジャスト・イン・タイムは、無駄を削減する上で重要なヒントを示す生産管理システムです。生産する製品の種類や数が安定し、生産ラインを滞りなく進められる場合、一度導入を検討してみるといいでしょう。
しかしジャスト・イン・タイムの実現には、前項で紹介した前提条件が欠かせず、導入までに多くの条件をクリアする必要があります。また、欠品のリスクや取引先への負担など、デメリットも少なくありません。理解が不十分なまま導入に踏み切った結果、生産ラインがストップしてしまい、大きな損害を出した企業もあります。
世界を席巻したトヨタのジャスト・イン・タイムは、製品の需要やサプライヤーとの連携など、巨大企業がひとつの生き物のように動くことに凄みがあります。
では、その他の製造業において革新的な業務効率化は難しいのかと言うと、そうではありません。現在、デジタル技術の発展で、中小企業でも大きな業務効率化を果たせる時代に突入しています。IoTやAIはもちろん、身近なところではタブレットの導入など、ITツールや最新のソリューションに業務効率化のヒントはたくさんあります。
働き方改革が求められている現在こそ、自社に適した業務効率化の手法を検討してみてはいかがでしょうか。