協働ロボットとは?従来のロボットとの違いや導入事例、最新動向について解説
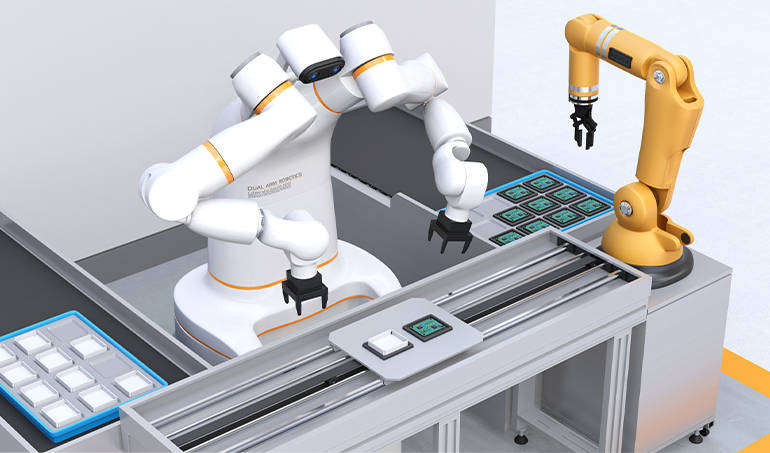
少子高齢化にともなう生産年齢人口および労働力人口の減少により、ロボットの活用に大きな期待が寄せられています。特に、製造業や食品業の生産工場などで活用される産業用ロボットは、これまで人が担っていた作業を自動化・効率化する選択肢として、急速に普及が進んでいる状況です。
その背景の一つとされるのが、ロボットの安全性の向上だと言えます。以前は産業用ロボットを工場などで使う場合、80W以上の出力を持つロボットについては周囲に安全柵を設ける必要がありました。しかし、2013年の労働安全衛生規則改定により規制が緩和され、80W以上でも安全柵なしで導入できるロボットが登場するようになりました。
本記事では、そんなさまざまな製造過程で活躍する「協働ロボット」について解説します。
協働ロボットとは?
協働ロボットとは、文字通り「人と協力して働くロボット」を指します。
たとえばパン工場を考えてみましょう。協働ロボットを使用する以前は、あんぱんの上に乗っている黒ごまを人力でまぶしていました。しかし、同じ姿勢で黒ごまをまぶす仕事をしていると、作業担当者は腰を悪くする可能性があり、また集中力の欠如などによってうっかり黒ごまを乗せないままラインを通過させてしまうというミスが発生するリスクがあります。
このような担当者の健康被害やヒューマンエラーのリスクに鑑みて、人の手で行われていた作業を代替する協働ロボットが開発されました。
協働ロボットを使うことで、より少人数で工場のラインを稼働でき、人手不足による稼働制限の解消や、生産性の向上へ大きく寄与することが期待されます。また、多くの場面で「非接触」での製造も可能になるので、ウィズコロナ時代におけるニューノーマルへの対応にも貢献すると言えます。
協働ロボットと従来のロボットとの違い
工場でのロボット活用は、最近になって始まったことではありません。これまでも、自動車や機械製造などの比較的大きな工場の生産ラインには産業用ロボットが組み込まれ活躍していました。
その後技術革新が進みロボットの小型化が加速します。ロボットが小さくなると、従来の大きな工場のみならず、より小規模な工場やラインでもロボットの導入が進むことになりました。
またAI技術などの発達によって、作業内容もより柔軟に対応できるようになります。たとえば先述したパン工場の例の場合、パンは機械と違って形状がある程度変化することを前提に取り扱う必要があるため、そのような形状のゆらぎに対応できるロボットである必要があります。従来のロボットでは事前に想定される形状に沿った動作をプログラミングすることになるので、形状のゆらぎがある対象物には不向きでしたが、AIなどを搭載したロボットの登場によってそのような柔軟な対応も可能となったのです。
さらに従来は、人の安全性を確保するために80W以上の出力を持つ産業用ロボットの周りには安全柵を設けることが義務化されていました。しかし冒頭に記載したとおり、2013年12月の規制緩和(厚生労働省「平成25年12月24日付基発1224第2号通達」)によって、以下の条件を満たすロボットである場合に限って、安全柵を設ける必要がなくなりました。
このように、ロボットの小型化とAIなどの発達による作業の柔軟性の向上、そして規制緩和が重なることによって登場したのが「協働ロボット」です。
協働ロボットの導入コスト
協働ロボットの導入には、以下のコストを考える必要があります。
ロボットの本体 | 協働ロボット本体の購入費用。 |
---|---|
周辺機器 | 協働ロボットの周辺に設置すべき機器の購入費用。たとえばアーム型協働ロボットの場合、指先となるグリッパーや、その付近に実装するエッジAI付きのカメラなどが挙げられます。 |
メンテナンス | 協働ロボットの保全行為にかかる費用。 |
導入コンサルティング | 協働ロボットを導入するにあたっての各種コンサルティング費用。協働ロボットはライン状にあるさまざまなロボットとデータ通信などをするケースが多いので、既存の機械の稼働状態に鑑みた導入設計が必要となるケースがほとんどで、そのためには専門家によるコンサルティングが不可欠となります。 |
人材教育・研修 | 導入した協働ロボットを活用するための社内人材への教育・研修費用のこと。 |
ロボットの本体価格は大きさや性能によってさまざまですが、一般的には200~500万円ほどとされています。従来のロボットは、安全柵の設置や強固な基礎工事が必要となり価格が1,000〜1,500万円程度であることを考えると、相対的に安いものだということが分かります。協働ロボットは大規模な工事をせずに移設でき、生産フローの変更にも柔軟に対応できます。
ただし、上述した各種コストが別途必要になるになるので、予算状況によっては購入ではなくレンタルやリースを検討してもよいでしょう。
参考:https://www.tak-robot-marketing.co.jp/contents/detail/collaborative-robot-cost
https://www.icom-giken.com/collaborative-robot-introduce-price/
協働ロボットの導入事例
ここからは、協働ロボットの導入事例についてご紹介します。
ラベルの貼り付け
石窯パンの製造をメインにさまざまな食品事業を展開する株式会社タカキベーカリーでは、協働ロボットとパラレルリンクロボットを組み合わせ、冷凍製品の解凍後の消費期限ラベル貼付けをする協働ロボットを導入しました。
これまでは人が手作業で製品にラベルを貼りつけていたものを、ロボットが完全に代替をするというものです。
出典:経済産業省「ロボット導入実証事業事例紹介ハンドブック2018」p12
これにより、生産性は2.5倍に向上し、人員を約半分(5人から2人へ)に削減。また、そのほかの効果として、消費期限ラベルを貼る品種や数量が多いことによる貼り付けミスの改善にもつながったとのことです。
全自動AI外観検査装置
オートバイ・農機用など各種歯車一貫加工を行う稲坂グループ(稲坂油圧機器株式会社)では、建機用の多品種油圧パイロット弁の最終検査である「外観検査」を、画像解析AIと協働ロボットによって自動化させました。
これまでは人による目視チェックをメインで進めていたため、検査を熟練作業者の感覚に依存する状況でしたが、それをAI×カメラを活用した協働ロボットによって自動化させたのです。
出典:経済産業省「ロボット導入実証事業事例紹介ハンドブック2018」p56
これにより、AIの活用による良品判定の実現に成功し、大きく生産性を向上させました。具体的には、同じ作業を行うための所要人員が1人から0.1人へと大幅に減り、生産性が10倍になりました。また、これまで熟練作業者が属人的に行わざるを得なかった作業も、より汎用的に対応できるようになったとのことです。
複数システムで兼用可能、導入費を低減
東洋ドライルーブ㈱はフッ素コーティングなど個体被膜潤滑剤の研究開発から製品製造・コーティング加工・販売までを自社で一貫して行っている会社です。今回ロボットを導入した愛知事業部はコーティング加工をメインとしており、自動車部品を数多く扱う工場です。しかし、扱う多くの部品で未だに人の手や目に頼る作業が工程内で大部分を占めています。
これまでもロボットの導入はされていましたが、生産量の減少と共に一日に数時間しか稼働しなくなっている等の経験もありました。そこで、移動可能かつ複数のシステムで兼用できる協働ロボットを導入し、コスト削減と業務の自動化を実現したのです。
出典:経済産業省「ロボット導入実証事業事例紹介ハンドブック2018」p78
協働ロボットは必要に応じてロボットを移動できるため、複数のシステムに兼用することで、少量多品種生産で投資回収不能であった製品に対してもロボットシステム化を実現します。これにより、生産性は2倍、必要人員は3人から2人となり効率化を達成しています。
協働ロボットの最新動向
出典:グローバルインフォメーション「協働ロボットの市場規模、2027年に105億米ドル到達予測」
最後に、近年の協働ロボットの最新動向についてお伝えします。
株式会社グローバルインフォメーションによる調査結果によると、協働ロボットの市場規模は2027年には105億米ドルに達すると予測されており、これから大企業のみならず、中小企業も含めて多くの企業が積極的に導入することが想定されています。
これは、協働ロボットの導入によって生産性が向上し、生産量の増加や製品品質の向上が期待できる点が大きな要因となっています。
従来のロボットより価格やコストが安価に抑えられるため、高い投資収益率を見込めるというわけです。
製造現場DXなら協働ロボット
協働ロボットは従来のロボットとは異なり、安全に人と共に作業ができるものとなっています。
従来は人の手で行っていた繊細な作業も協働ロボットで代替可能であるため、人件費の削減や技能継承にも貢献すると考えられます。
今後、市場規模が飛躍的に拡大することが見込まれており、ますます導入企業が増えると予測されます。
製造現場DXを目指す企業は導入を検討してみてはいかがでしょうか。