ピッキング作業を効率化!実現する手法とポイントを紹介
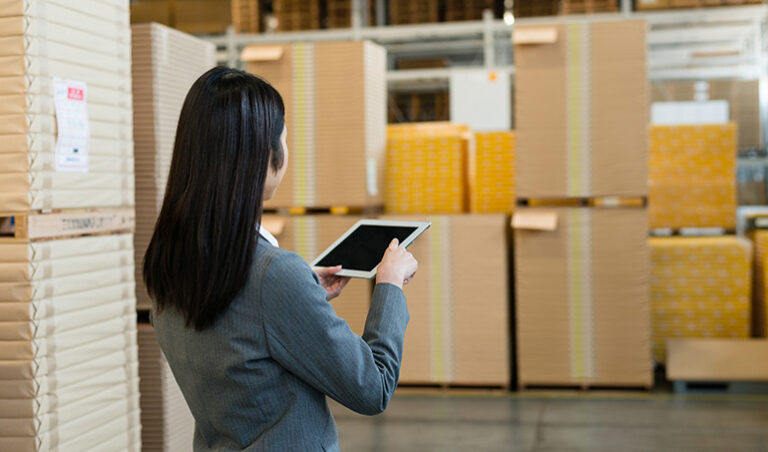
物流倉庫における仕分けやピッキング作業には、正確さとスピードが求められます。また近年では、EC化の影響で、多品種少量を多頻度で輸送しなくてはいけないケースも多く、倉庫での業務効率化がより求められています。
倉庫における仕分け、ピッキング作業はどのように効率化、スピードアップを図り、ミスを減らせばいいのでしょうか? 今回は最新事例を紹介しながら、ピッキング作業の業務効率化のヒントを紹介します。
仕分け・ピッキング作業とは?
仕分け・ピッキング作業とは、倉庫から商品を出荷するのに必要な作業です。出荷の内容によって、業務の流れや役割、方法が変わってきます。改めてピッキング作業の目的や手法を紹介します。
物流における集品(ピッキング)の役割と目的
ピッキングとは、顧客から注文を受けた商品を、倉庫から取り出し、出荷できるよう品揃えをする一連の作業を指します。
倉庫から必要商品を取り出して、出荷ができる状態にするために仕分けとピッキングが行われます。顧客からの受注伝票や出荷伝票を見ながら、商品を広い倉庫から取り出し、台車やコンベアを使って1つの場所に集約しなければなりません。ただし倉庫によっては、1日に取り出す商品の種類や数、伝票枚数は多岐にわたり、限られた人数と時間の中で、効率よく商品をまとめなければいけません。特に近年ではEC市場の拡大に伴い、多種の商品をできるだけ早く発注者の元に届けることが求められており、倉庫における効率化は大きな課題となっています。
ピッキング作業の手法
ピッキング作業は大きく2つの方法に分けられます。ここでは「摘み取り式」と「種まき式」の2つを説明します。
【摘み取り式】
摘み取り式とは、注文先別に商品を取り出す方法です。同じ商品を1度にまとめて取り出すのでなく、注文先別に順番に取り出すため。主に取り出す商品の種類が、注文先の数より多い場合に活用されます。注文先ごとにピッキングして、梱包する単位ごとに商品を集めるため、取り出すべき諸々の商品が「多品種少量」の場合に適しており、オーダーごとに取り出してすぐに出荷できる長所があります。「シングルピッキング」や「オーダーピッキング」とも呼ばれます。
【種まき式】
種まき式とは、必要な商品をまとめて取り出したあとに、注文先別に仕分けるやり方を指します。先に必要商品をすべて取り出してから、出荷先別に仕分ける作業工程のため、主に取り出す商品の種類が、注文先の数より少ない場合に活用される方法です。1度に商品をすべて取り出すため、シングルピッキングと比べて移動時間を削減することができますが、後から注文先別に仕分けなければいけないため、作業工程がひとつ余分に増えることになります。「トータルピッキング」とも言います。
仕分け・ピッキング作業の課題
仕分け・ピッキング作業は正確さとスピードが求められます。しかし、膨大なオーダーと商品を広い倉庫から取り出すため、どうしてもピッキングミスが発生してしまいます。ピッキングミスは物流倉庫では、業務効率化と並ぶ永遠の課題とも言えるでしょう。そのため、業務効率化とミスの低減は同時に進めていく必要があります。
ピッキングミスは本来出荷すべき商品とは違うものを取り出す、もしくは出荷数を間違ってしまうことがほとんどです。人間による作業ですから、二重三重のチェック体制でもヒューマンエラーが起こってしまいます。
特に紙のリストを使って目視を頼りに商品を整理するピッキングでは、似たようなパッケージや品番の商品を混同してしまうミスが発生します。品番を読み間違えて違った商品を取り出してしまう、仕分けの際に違うカゴに投入してしまうなども多く発生しやすいヒューマンエラーです。
ピッキングミス・誤出荷の原因は倉庫環境にある
こうしたヒューマンエラーを防ぐには、一般的には、ダブルチェックの徹底や従業員の意識向上などの対策が講じられることが多いですが、やはり作業の担い手が人間である以上、ミスを「ゼロ」にすることは現実的に難しいでしょう。しかし、倉庫環境を見直すことで、ある程度のピッキングミス・誤出荷を低減することができます。例えば、リストの品番表示や動線のムダなど倉庫環境を見直すことで、ミス削減と業務効率化の効果を期待できます。
ルート・動線の最小化
商品をピッキング・仕分けるルート・動線を最小化すれば、1人当たりの移動時間が短くなります。移動時間が短くなった分、業務効率化ができますし、従業員は疲弊を抑えることができ、注意力を保ったまま業務にあたることができます。
無駄な作業の削減と平準化
リストが見づらくないか、どう変更すれば見やすくなるかなどの工夫を凝らすことも大切な解決策です。ピッキングの指示をできるだけわかりやすくするなどオペレーションを改善することで、初心者からベテランまで作業のクオリティを一定にする効果があります。
ロケーションの徹底管理と見直し
倉庫内のどこに何があるのかを、作業員が把握しやすくする必要があります。倉庫が広ければ広いほど、ロケーションを管理しているかどうかで業務効率の差が出ます。ピッキングミスを防ぐために類似商品の棚は遠ざける、出荷頻度が高い商品は出荷口付近に保管するなどちょっとした工夫でミスを防止しながら、業務効率を実現できます。
物流業界のデジタル化で業務効率は進む!
物流業界は、世界規模でICT、IoT、ビッグデータなどを駆使した技術革新の渦中にあると言えます。国内でも、少子化による人手不足といった社会構造の変化に伴い、1人当たりの生産性向上が必須であるため、さまざまな構造変革が起きています。このような技術革新は「ロジスティクス4.0」と呼ばれています。
「ロジスティクス4.0」の4は、第4次産業革命(インダストリー4.0)の物流版という意味で名付けられました。これまでにも物流業界には、トラックの実用化や荷役の自動化、物流管理のシステム化といった大きな変革がありましたが、「ロジスティクス4.0」では、IoTの進化とともに「省人化」と「標準化」が進もうとしています。例えば、今回テーマとしているピッキング作業も将来的にはロボットにより自動化されると言われています。
仕分け・ピッキング作業も最新ツールで効率化できる
「ロジスティクス4.0」の説明をしましたが、無人ロボットなどの実用化はまだ少し先の話になりそうです。無人化とまではいかなくても、ピッキングの業務効率化を実現するツールは数多く存在するので、いくつか紹介します。
●次世代バーコードの活用
1枚1枚手動でスキャンする従来のバーコード管理の先をいく「次世代バーコード」は、一度に多くのバーコードをスキャンできるため、大きな業務効率化が期待できます。代表的なものが電波を使った「RFID」です。
例えば、荷棚の大きな段ボール箱が20箱積まれている場合、旧式のバーコードリーダーなら脚立を使って一箱ずつスキャンしなければいけません。一方、「RFID」なら荷棚の前で機器をかざせば、電波が20箱分のバーコード情報を拾ってくれます。電波を使うので、箱の中に隠れているタグも読み取ることができます。また中にはトレーサビリティ機能が付いたRFIDもあります。
●ハンディターミナル・タブレットピッキング
ハンディターミナルとは、商品情報をスキャンで読み取る携帯型の機器のことです。データをリアルタイムで収集・処理でき、ピッキング業務では、品番のミスを防ぐことができ、スキルや経験による作業のムラを防ぐこともできます。またタブレット端末でデータを共有すれば、ピッキングの状況を逐次管理することも可能です。
●音声ピッキング
音声ピッキングとは、ハンディ機器などを使わずに、ヘッドセットを装着して、音声による指示・確認でピッキング業務を行うやり方です。音声の活用により、確認作業とリスト記入作業の時間を削減することができます。
まとめ
ピッキング作業はこれまで手作業に依存していた側面が強く、リストの目視、手作業による商品の取り出し・仕分けで、人的リソースを割くため、どうしてもミスが出てしまう課題がありました。
しかし、デジタル機器の活用により、品番や品数を間違えるといったヒューマンエラーを防ぎ、かつ作業効率を大きく上げられることをお伝えしました。電波を使った一括スキャンや、音声でピッキング情報を出入力する音声ピッキングなど無理のない範囲で導入できるツールはたくさんあります。現場の実情に合ったツールをぜひ導入してみてはいかがでしょうか。