リードタイムの短縮で業務効率化を実現する手法とは!?
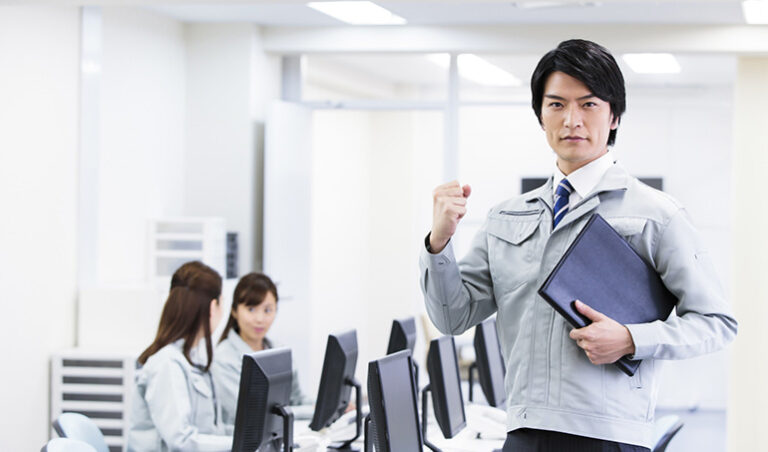
ニーズが多様化・細分化した現代では、単一品種大量生産や多品種少量生産に対応しながらもよりフレキシブルに変種変量生産やJIT(ジャスト・イン・タイム)生産を目指さなくてはいけません。同時に自社の製品やサービスを、製造からエンドユーザーの手元に供給するまでのスピードをいかに迅速にできるか。サプライチェーンの安定は、すべての製造業が取り組むべき課題です。
そのため競合他社に先駆け、顧客が求める製品やサービスをいち早くリリースしていくために、各社が鎬を削っている状態ですが、どのような手段が考えられるのでしょうか?
今回は、サプライチェーンの効率化に不可欠な「リードタイムの短縮」について、製造業が取り組むべきことをまとめました。
在庫管理とリードタイムの関係について
リードタイムとは、広義では製品の開発に始まりエンドユーザーのもとへ製品・サービスが届くまでの期間を指します。業種や企業によって異なりますが、各工程によってリードタイムが設定されています。一般的にリードタイムを分けると下記の4つとなります。
①開発リードタイム……製品の研究・開発にかかる期間
②調達リードタイム……製品の製造に必要な材料を集める期間
③生産リードタイム……製品を製造する期間
④配送リードタイム……出荷からユーザーの手元に製品が届くまでの期間
それぞれのリードタイムを詳しく解説します。
①開発リードタイム
製品の研究・企画・開発にかかる日数、所要時間です。冒頭で説明したように現在の市場ニーズは目まぐるしく変化しているため、市況を把握してから開発、製造に着手できる期間を短縮できるほど、結果的に他者より早くタイムリーに製品を市場に投入することが可能となり、その分利益を得ることができます。「標準化・モジュール化」や「オープンイノベーションの促進」、市場ニーズの把握・調査、研究開発費など多くの要素が複雑に絡みますので、開発リードタイム短縮は簡単ではありません。しかし、最終意思決定者を誰が担うか、という点は課題解決となりそうです。ニーズを把握しても「GO」サインが出なければ、どうしても初動が遅れてしまいます。企画・マーケティング部門がない企業では、経営層が判断することが多くなっていますが、市場ニーズを把握する専門部署、もしくは担当者に権限委譲することでスピーディな判断が可能になります。
②調達(購買)リードタイム
製品の材料などを発注してから受領するまでの期間を指します。サプライヤーの選定から納入、検査・検収などの一連のプロセスがあり、価格、在庫、品質、納期などの観点が必要となります。製造業では原価のほとんどが材料費になることが多く、かつ一定量を発注しなくてはコストが高くなります。購買・調達管理の仕事はここを調整することと言ってもよいでしょう。そのため調達リードタイムでは、サプライヤーとの関係性が非常に重要になってきます。サプライヤーに納期を短くして、と依頼しても解決しませんので、サプライヤーの生産工程や生産サイクルを理解して、パートナーとして密な関係性を構築していくことが不可欠となります。
③生産リードタイム
製造に必要な部材をそろえ、それらを組み立て最終的に出荷できるまでの状態にするリードタイムで、「生産リードタイム」や「標準日程」とも呼ばれます。実際の製造ラインに携わるスタッフの力量が問われる分野でもあり、製造工程の中であらゆる無駄を洗い出し、適切な人員配置や、使用する機器や道具の新調、メンテナンスといった効率化を図っていくことが求められます。
「〇時間内に〇個の製品を作る」といった数値で表されるルールや目標がある場合には、「タクトタイム(またはピッチタイム)」が用いられます。タクトタイムが正確に守られれば、前後の工程においても決まった数量が把握できるため、工場全体の効率的な操業に寄与します。しかし、無茶なルールを設けてしまうとスピードを追求してしまい、無理な作業が生じ不良品や事故・ケガの発生にもつながりかねません。結果として生産性が下がるので、適正な目標値を設定する必要があります。またタクトタイムとは逆に、1つの製品を製造するのにかかる時間を「サイクルタイム」と言います。サイクルタイムは作業効率を図る際の基準となりますので、必ず把握しておきましょう。
また、自動車や産業機器などの大がかりな製品ではサプライヤーも多岐にわたるため、②の観点でも説明した通り、欠品や遅配・誤配を発生させないよう、各取引業者との連携を綿密に図っておくことも重要です。
④配送(出荷)リードタイム
実際にエンドユーザーからの注文を受け、発注主の手元に届くまでにかかる期間です。これは生産方式によって大きく異なります。
STS(Sales to Stock)
小売店などが抱えている在庫の中からエンドユーザーに販売する方法です。コンビニでジュースやタバコを購入するように、店舗やネット通販で即座に買い物できる仕組みです。
MTS(Make to Stock)
「見込み生産」のことで、メーカー側が事前に予測を立てて生産数を決める手法です。注文が発生した場合でも、在庫があれば比較的早く製品が供給できます。
BTO(Build to Order)
「受注加工組み立て」のことで、注文があった時点で生産を開始します。そのため、事前に材料をストックしておく必要があります。ベースとなる中間品をあらかじめ組み立てておき、注文ごとに細かなアレンジを施して出荷するATO(Assemble to Order)という方式もあり、こちらの方がよりリードタイムは短くなります。
MTO(Make to order)
「完全受注生産」で在庫を持たないのが特徴です。企業側としてはコスト的には有利かもしれませんが、部材の調達を一から行うため当然リードタイムは長くなります。一般ユーザー向けで言えば、戸建ての注文住宅がこれに該当します。
リードタイムは在庫管理と密接な関係にあります。製品を過剰に製造すればコストの圧迫につながり、逆に少なければ欠品につながるため、代理店や販売店、そして最後に製品を購入する一般ユーザーからの信頼を大きく損ねることになります。そのため在庫管理はどの企業でも頭を悩ませる問題であり、リードタイムを知ることは自社の市場への対応力を知ることにもなります。
リードタイムを短縮するための基本的な4つの手法
では、製造業におけるリードタイム短縮のためにできる基本的なアクションを紹介します。業務の効率化を図るために、まずはどこから着手できるか、下記を参考にしてみてください。
増員
シンプルなのは人員を増やすことです。生産量と適正工数、サイクルタイムから必要人数が割り出されているのが一般的ですが、繁忙期や超短納品などの場合、増員をするケースが考えられます。増員をすることで生産量は上げることができるので、非常に有効です。しかし、短期的な視点ではなく、中長期で計画を立てなくては、人件費のムダが生まれてしまうリスクがあります。販売予測と工場全体の生産量、投入工数を検討して、余剰人員が出ないように工夫しましょう。
不良率の削減
製造の段階で不良品が出れば、いったんラインを止め原因究明にあたることになり、リードタイムに悪影響が出ます。例えば、製造の過程で検品のタイミングを設け、不良品を迅速に発見しすぐに対処できるようにすることでロスは減らせるでしょう。また、長期的な取り組みになりますが、実作業にあたる技能工の技術指導といった教育プログラムを定着させていくことも大きな効果を生むはずです。
作業工程の合理化
作業時または前後の工程で合理化を図る手段です。例えば、設計を標準化し、使用する部材も共通の規格のものを使用する。こうすればロット数の変更やまったく同じ製品を別のラインで製造する場合にも即座に対応できることでしょう。また、製造時に使う部材についても、事前にその数を把握し用意しておきたいところ。いざ製造が始まった際に、部品を探す時間やストックヤードから運んでくる時間を省くよう徹底しましょう。
最新機械の導入
現在、急速に工場のオートメーション化が進んでいます。使用する機械を最新のものにアップグレードすることで、作業効率を向上させることも効果的な手法の1つです。人的リソースでは、どうしても予期せぬ欠員が発生する可能性があり、技量にもばらつきが生じますが、機械の導入は一定のパフォーマンスを約束してくれます。ただ設備導入にはコストがかかります。また専門知識があるスタッフの育成が必要なケースもあるため、メリットとデメリットを精査して検討しなくてはいけません。
デジタルツインの導入で、諸問題をリアルタイムで洗い出す
経済産業省が推進する「Connected Industries」やドイツの「インダストリー4.0」など、製造業では、AIやIoT、ICTを活用したスマートファクトリーを目指すのが、世界的な潮流となっています。
具体例として、蓄積されたデータを有効活用する「デジタルツイン」によって実現するリードタイム短縮について紹介します。
デジタルツインとは、実際に存在するモノの動作をセンサーで読み取り、デジタル空間でその動作を再現する手法を指します。現実そっくりのモノの動作をデジタル空間のシミュレーションで再現させるため、「双子(ツイン)」という名前が付けられています。
最大のメリットは、各工程でさまざまなシミュレーションが可能になることです。機械のトラブルや不良品が生じた場合、いったん製造ラインをストップさせてから原因を追究する時間が生じます。操業中の機械をそのまま確認することは不可能なため当然の措置と言えますが、デジタルツインならばリアルタイムで機械や製作途中の製品のモニタリングができるため、故障や不良個所をすぐに発見できます。またデータを蓄積していくことで、課題を明確に抽出することができ、予防保全も可能となります。
ドイツに本社を置くシーメンスでは、製品の製造段階でデジタルツインを導入し、不良品の発生につながる金型の劣化をいち早く検知できるようになりました。多彩なチャネルを持つ同社では、工場でのデジタルツイン化を急速に進めており、事前のシミュレーションで万全を期してから実際の工程に落とし込むことでリードタイムの短縮とコスト削減を目指しています。
<参照:Siemens PLM Software>
タブレットがリードタイム短縮に効果的
大企業が採用するようなデジタルツインやスマートファクトリー化は難しいかもしれませんが、手に入りやすい身近なデジタル機器で業務の効率化を図ることは可能です。現在、一般的に普及しているタブレットがその1つです。
現在、製造業における在庫管理システム、倉庫管理システムなど、ソフトウェアやクラウド型サービスは多くあります。タブレットであれば、パソコンやノートパソコンとは異なり、工場内を歩き回りながら使用することが可能です。製造ラインにおけるデータ収集、記録から報告など現場と本社間でリアルタイムに共有することができるので、大きな業務効率化を期待できます。
カメラ機能が付いていれば、トラブル箇所や不良品についても瞬時に撮影し、正確な情報を共有することができます。従来はペンと用紙で記録を行い、事務所に持ち帰ってから記録内容をパソコンに入力するといった流れでしたが、タブレットがあれば時間短縮とペーパーレス化による経費削減につながります。また、営業や打ち合わせなど工場外の業務においても、必要に応じてデータを瞬時に表示させることができるため、商談や会議などもスムーズに行うことができるでしょう。
このような業務用のタブレットは、防水・防塵加工が施されているものを選ぶと、過酷な環境下が予想される工場でも安心して使うことができます。また、耐薬品性能を向上させたモデルも登場しており、アルコールなど薬品を用いたふき取りも可能で、メンテナンス性を含めて高いパフォーマンスを発揮します。
まとめ
リードタイムは製品の開発からエンドユーザーに供給されるまでのトータルの期間を指すため、ひと口に“短縮”と言っても複雑な工程のどこから手を着ければよいのか、瞬時に判断が下せるものではありません。
それだけにタブレットなどのデバイスは、導入するだけで一定の効果を期待できます。特に在庫管理システム、販売管理システムなどを導入している企業ならば、より高い効果が期待できるでしょう。リードタイムの短縮という課題に対して、工程を分解していくと具体的な対策は見つけることができるかもしれませんが、タブレットの導入はリードタイム全体に常に発生する報告、共有など細かい業務に対して有効です。
今後の製造業のデジタル化はより加速していくことが予想されますが、その一歩目としてまずはタブレットの導入から始めて、現場のモチベーションアップを試みてはいかがでしょうか?